Pivoting Toward PPE
Temple's collaborative approach toward COVID-19

Driven by Temple’s commitment to collaboration and creating solutions, the interdisciplinary Temple University COVID-19 Assistance Team (TUCAT) assembled to fashion personal protection equipment (PPE) for frontline workers in the Temple University Health System. As COVID-19 swept the nation, the globe, and Temple’s hometown of Philadelphia in Spring 2020, the critical PPE shortage presented an unprecedented challenge.
At the onset of COVID-19, the $4.5 million, 8,000-square- foot IDEAS Hub at the College of Engineering stood ready for students to use as a creative workspace, outfitted with the industry’s latest tools: robotics, drones, and 3D printing. Photos capture the grand opening of the facility in February, as proud faculty and staff stand side-by-side, unmasked, to cut the ribbon.
What the IDEAS Hub would become in the months that followed is something few could have predicted: a dynamic production center where a team of students, faculty, administrators, and volunteers would manufacture PPE in support of Temple’s Health workers amidst a global pandemic.
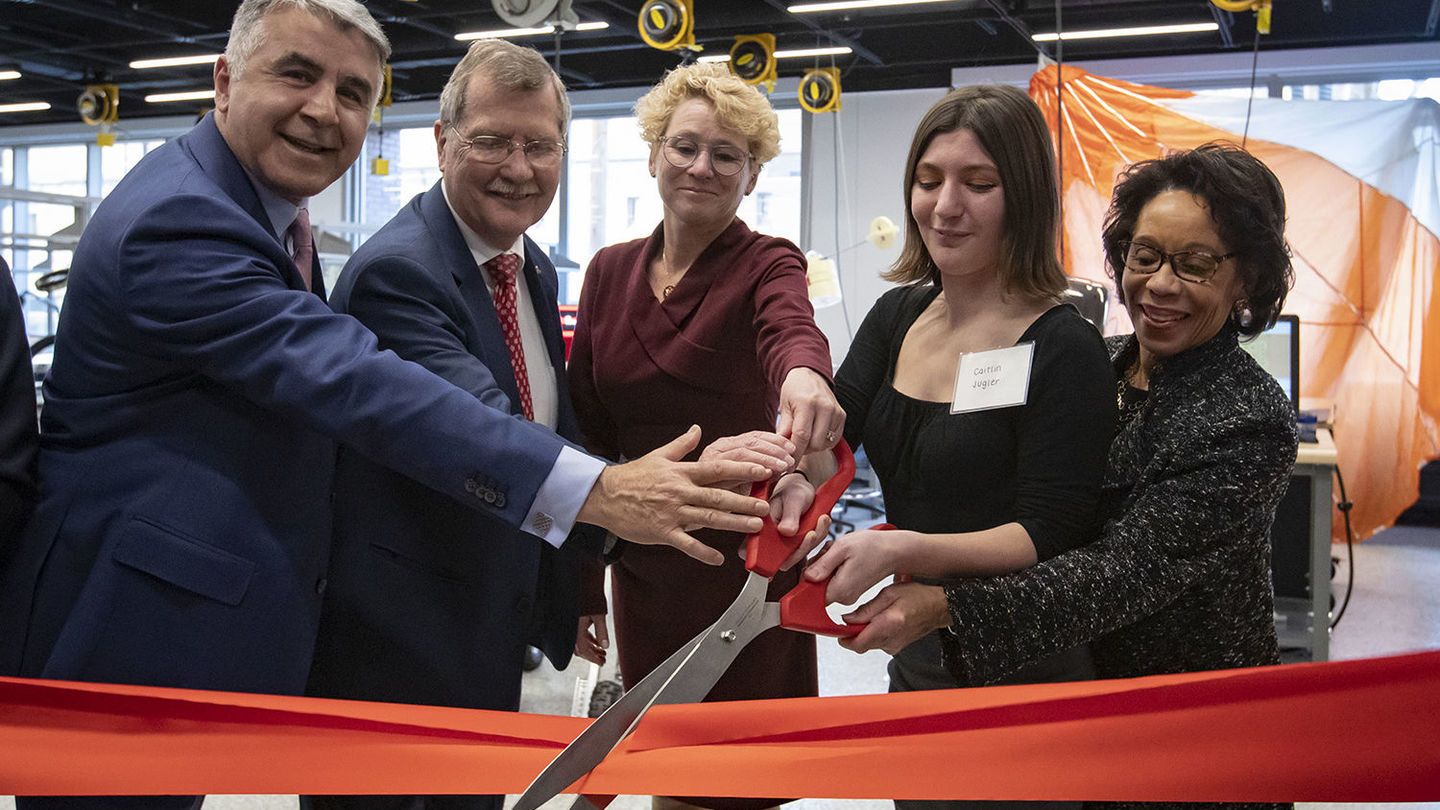
L-to-R: Dean Keya Sadeghipour, President Richard Englert, Rep. Chrissy Houlahan, Caitlin Jugler, Provost JoAnne Epps PHOTO: RYAN BRANDENBERG, TEMPLE UNIVERSITY
L-to-R: Dean Keya Sadeghipour, President Richard Englert, Rep. Chrissy Houlahan, Caitlin Jugler, Provost JoAnne Epps PHOTO: RYAN BRANDENBERG, TEMPLE UNIVERSITY
Armed with a limited supply of single-use masks, Temple University Hospital was quickly overwhelmed by COVID-19 and the race for protective gear. Bill Wohl, a Temple University Hospital (TUH) organ transplant coordinator, witnessed it first-hand. “You’re competing not only with every other hospital in your area, but entire countries that are coordinating national responses to get people what they need,” he says. “We had a humongous challenge.”
Temple University announced the suspension of in-person classes on March 11, shifting to online coursework the following week. Within two weeks’ time, Mayor Jim Kenney and the City of Philadelphia would issue a stay-at-home order as the number of positive COVID-19 cases numbered in the thousands, with the highest concentration in Philadelphia County. With the campus and the city closed, Temple Hospital enlisted the help of the university with an initial request of 10,000 protective face shields.
Phil Ryskalczyk, an undergrad in the engineering technology program and employee in the College’s IT office, was tapped early on in the project for his manufacturing expertise. He and Mike Kala'i, the Senior Director of Technology and Operations and the lead of what would become TUCAT, set to work.
“[The project] started with 3D printing and grew into something a lot larger because the number of the requests were higher than we expected,” says Ryskalczyk. The face shields were composed of three main parts: a plastic piece to cover the face, a headband, and an elastic band to keep the shield in place during use. Early iterations of the shields were made of foam and plastics glued together with materials from Home Depot and 3D-printed headbands.
Initially, production was time-consuming, sometimes taking up to an hour and a half to produce a single shield. “We were making what we could because we knew they needed things as soon as possible,” says Wohl, whose decade of experience as a frontline worker informed elements of the design. “All of the businesses around us were closed and shipping times were delayed, so it was hard to get parts.”
The team eventually found sources for reusable plastics that could survive the wear and tear of the emergency room, and thus turned their attention to perfecting the model. But they were still racing COVID-19 and the clock.
“Once we realized we wouldn’t be able to hit our target with 3D prints, that’s when it became a multidisciplinary group,” Ryskalczyk says. After a first run of about 250 face shields to fill hospital stop gaps, the team pivoted toward a solution to meet the increasing demand: More hands on deck.
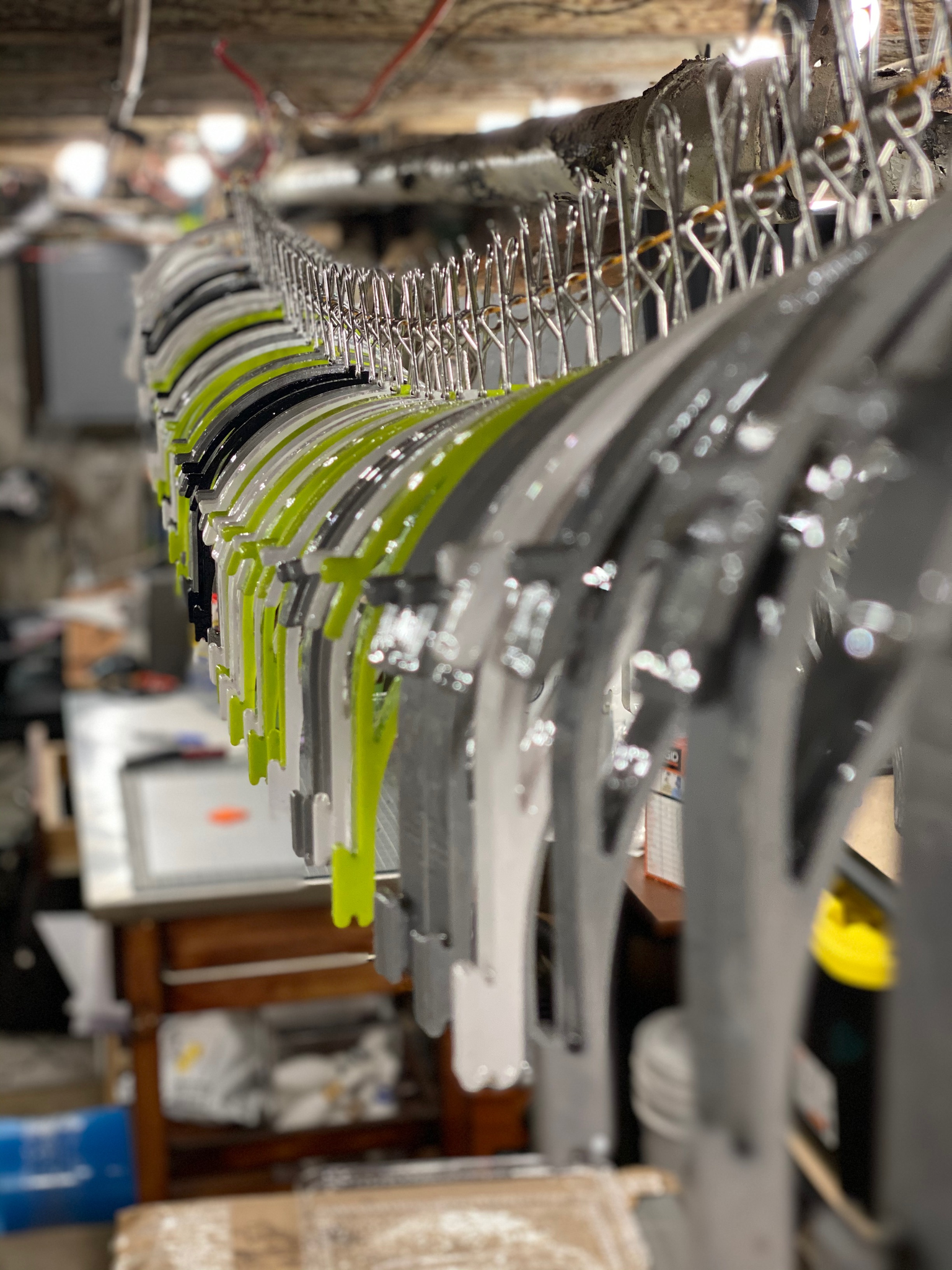
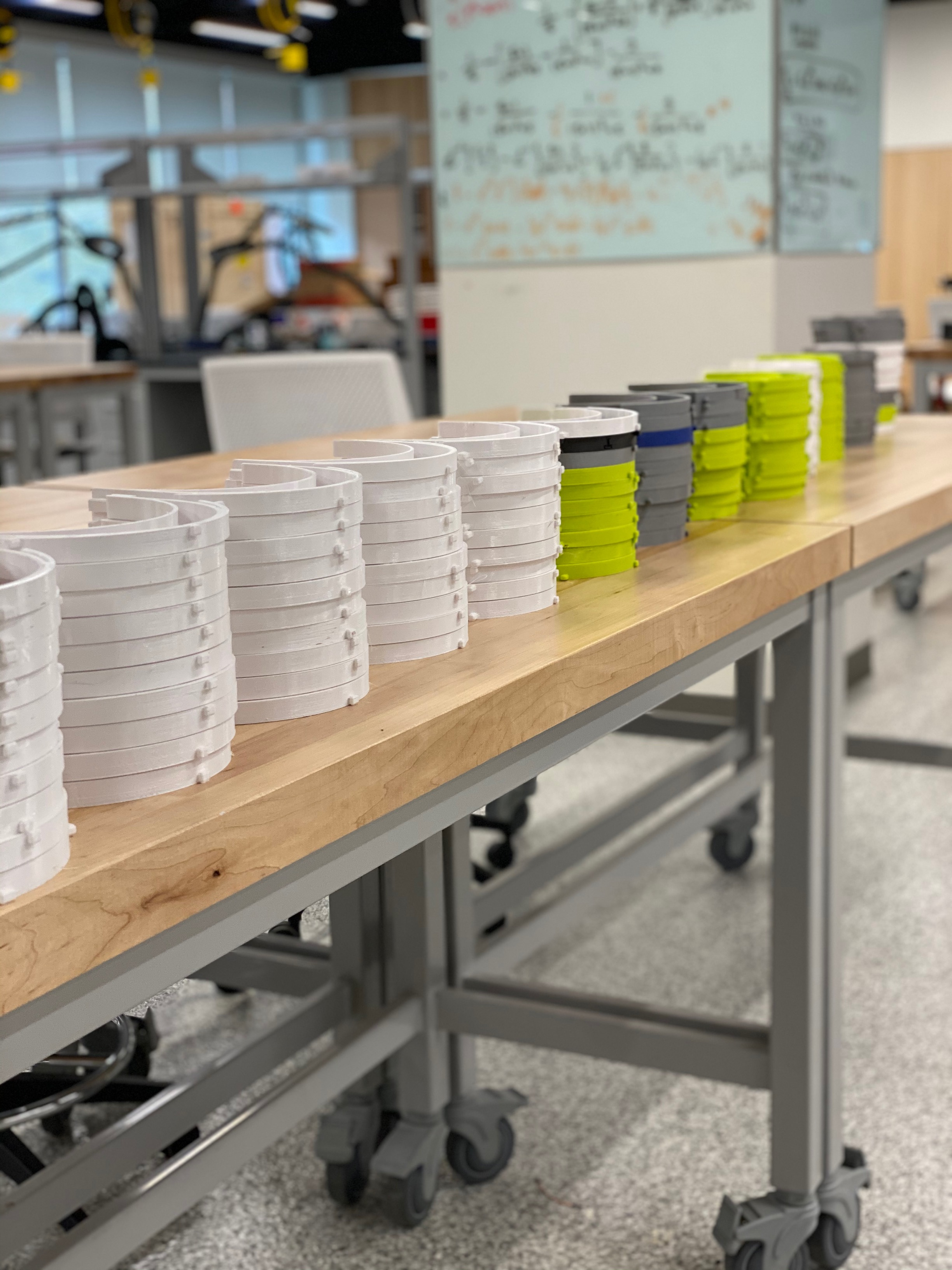
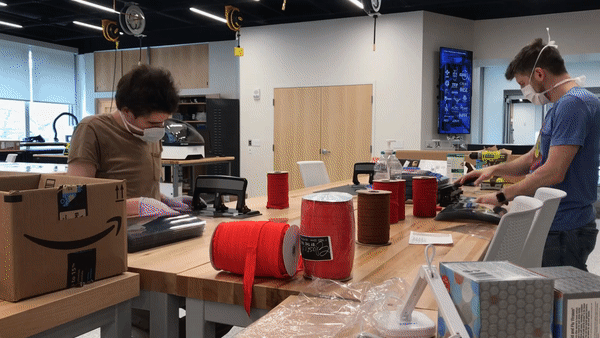
Jack Oswald, Phil Ryskalczyk and Bill Wohl (L-R) during an assembly session during the early days of the task force.
Jack Oswald, Phil Ryskalczyk and Bill Wohl (L-R) during an assembly session during the early days of the task force.
TUCAT quickly grew to include a rolling cast of contributors from Temple’s College of Science and Technology, the Tyler School of Art and Architecture, Temple Libraries, Temple Health and the Office of the Vice President for Research, many of whom were students in the midst of end-of-semester finals and exams. With safety in mind, individuals working in the Hub were required to wear masks, maintain a 15-foot distance at work stations, and have their temperature taken before entering or leaving. Hannah Alexander, a pre-med student, worked as a project coordinator, keeping a record of each individual working on-site.
Together, the expanded TUCAT began producing its own face shields, implementing a new mold design and workflow that could make up to 24 headbands within 40 minutes. The group used 3D printed shield holders to create traditional poured-plastic molds that allowed for mass production.
They would go on to produce 16,200 face shields at well below the estimated cost. In the spirit of collaboration, the team has since made the TUCAT designs available online for download, which have already been used by other institutions, as well as video walk-throughs of many design iterations hosted on tucat.temple.edu.
Ryskalczyk credits the final design to the teamwork. “A lot of the [process] is kind of boring or mundane work. It’s sanding the bottom of things. Trimming edges. It’s a lot. We had volunteers who did a lot of that important work and helped us finish up and get through the rest of things. It’s a team effort and we wouldn’t have been able to get through it without [help].”
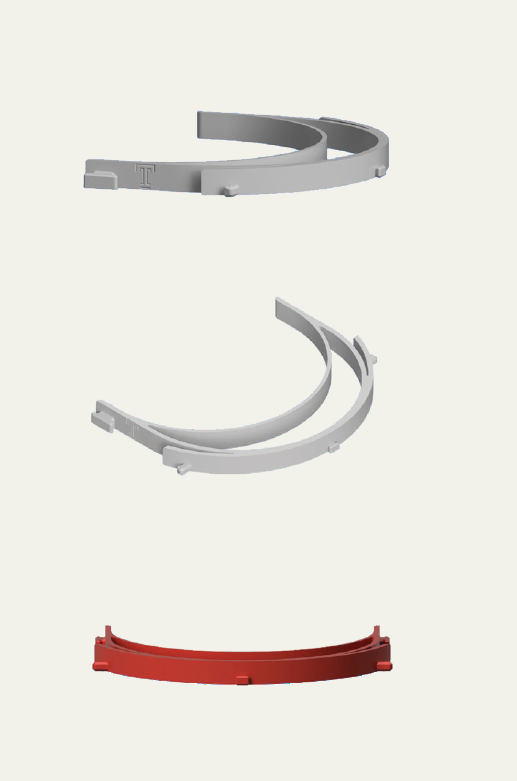
Renderings of the head band portion of the face shield assembly.
Renderings of the head band portion of the face shield assembly.
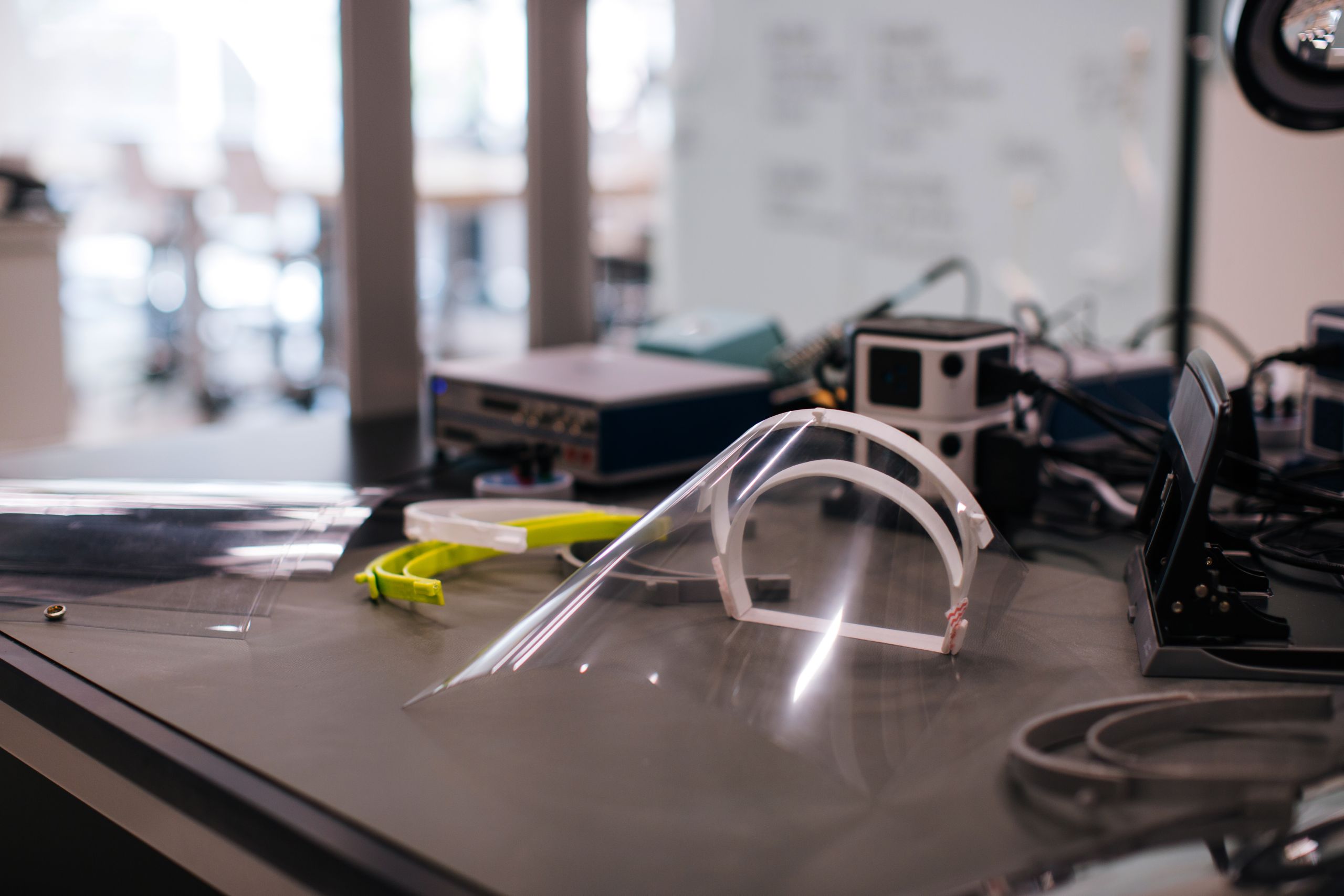
A completed face shield.
A completed face shield.
“We’re Temple people. This is what Temple people do.”
Temple Hospital Transplant Coordinator Bill Wohl
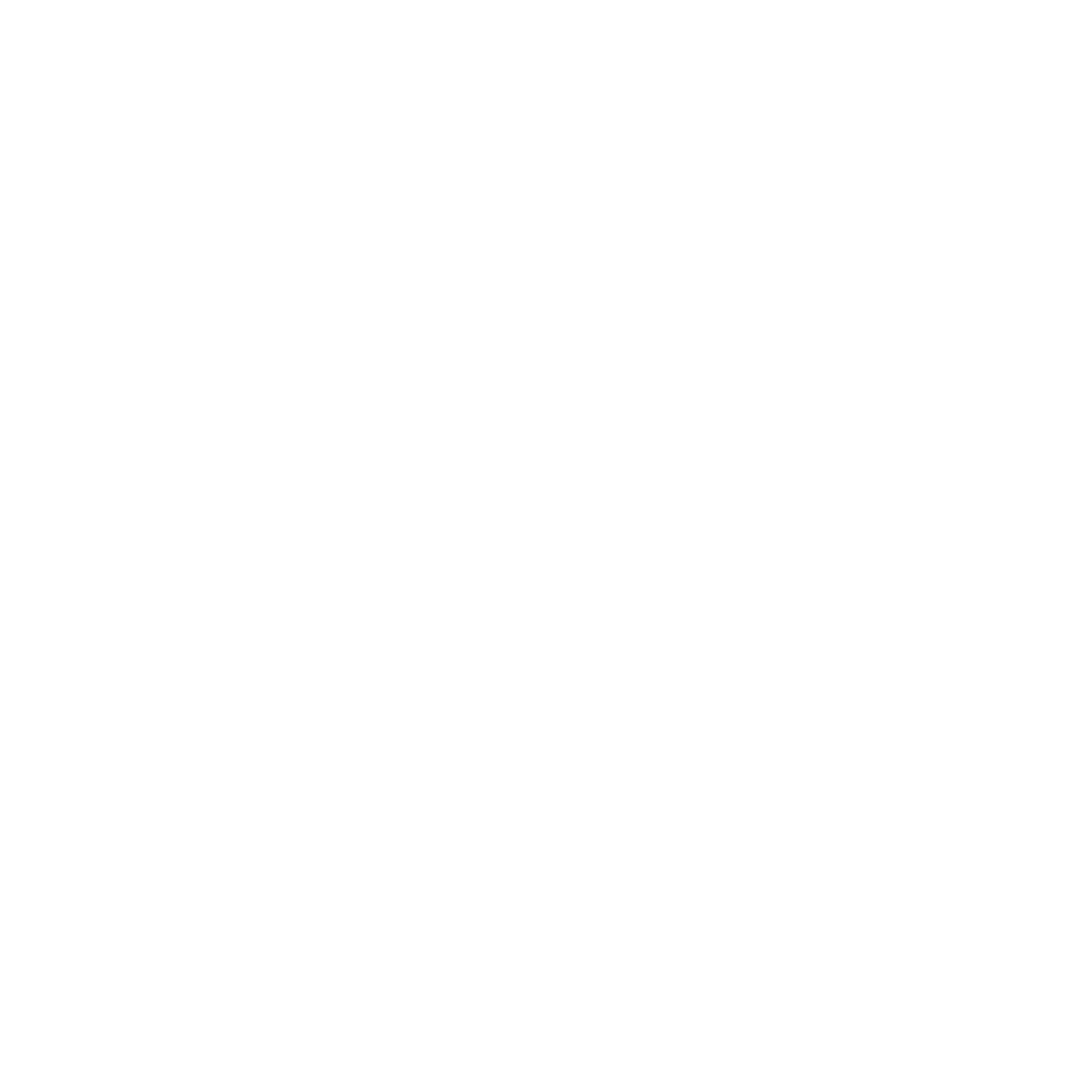
According to Susan Oldfield (pictured at right), a bioengineering student and Vice President of TemPO, a student organization that creates prosthetic and orthotic devices, there were no “gatekeepers” in the planning meetings, allowing for a free exchange of ideas and information.
“Engineers have the tendency to look inwards and there’s an innate kind of...We all think we’re pretty great,” Oldfield laughs. “Sometimes there’s a tendency to discount other opinions. I think the strength of this group is that it was that everyone was [welcome]. The diversity of thought and opinion made [us] very successful. I think all of us in the College of Engineering are really blown away by what everyone else did.”
Today, TUCAT stands ready to go back into production in case of another wave of coronavirus infections. While team members have wound down production for now, they continue to iterate their designs remotely, ready to take on another large order of PPE.
“There are a few changes that would boost our efficiency, but we would be able to spin up some form of production in about a week,” says Ryskalczyk. “We’ve been having conversations and testing things to make sure they’re ready to go.”
TUCAT credits the university’s willingness to innovate during a time of crisis, celebrating the unique opportunity and responsibility they were given to work while the rest of the campus was shuttered. When students enter the IDEAS Hub in the fall, some for the first time, they’ll enter a space already alive with Temple’s changemaking ethos. “We’re Temple people,” says Bill Wohl. “This is what Temple people do.”
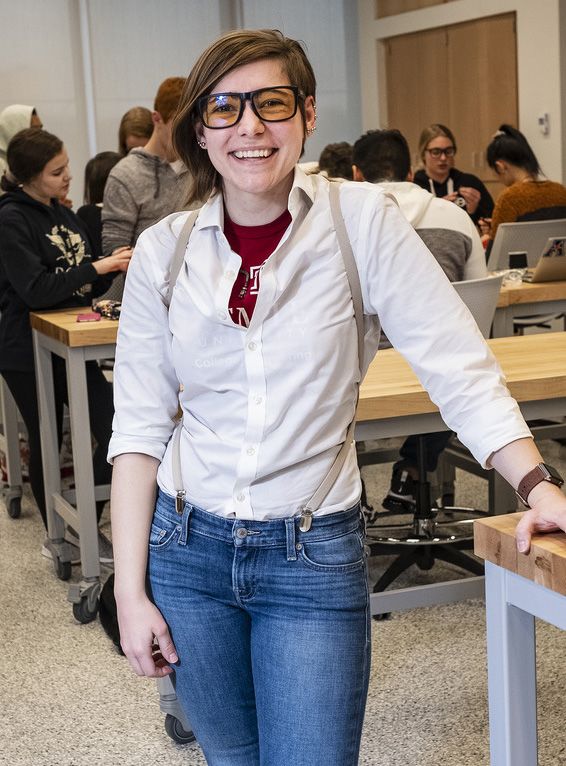
Susan Oldfield in the IDEAS Hub.
Susan Oldfield in the IDEAS Hub.
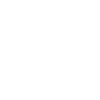